SERVICE FOR NITROGEN SYSTEMS & PSAL® - SYSTEMS
QUICK & RELIABLE SERVICE & MAINTENANCE FOR SYSTEMS & COMPONENTS
As the manufacturer, AIRCO® offers you comprehensive service for the technical maintenance of your nitrogen system. In addition to the maintenance of PSAL® systems, we can of course assist with additional areas and advise you comprehensively on topics such as the preparation of refrigeration and adsorption technology, energy efficiency and cost savings. We also offer a system installation service. You will benefit from our many years of experience in nitrogen, compressed air and oxygen production.
Our PSAL® system is a low-maintenance product. Nevertheless, it must be inspected regularly for maintenance purposes.
Depending on the particular system, a technician will visit you either annually or as per a service interval and will subject your system to a comprehensive inspection. We are in continuous contact with our customers for this purpose and our emergency service is available around the clock.
Our remote monitoring box allows us to pro-actively contact our customers in the event of possible malfunctions and to provide support during troubleshooting. Moreover, we offer bespoke maintenance contracts. For the fault-free and smooth operation of our PSAL® systems, the following points, for example, are usually checked on a daily basis through to an annual basis:
- The refrigeration dryer
- The filtration unit for wear
- The measurement values, quality and purity of the nitrogen
- The high-pressure compressor for wear
- The activated carbon is checked and replaced if necessary
- Rotary compressors from the leading manufacturers Mattei and CompAir
- Screw compressors from Atlas Copco as well as all reputable manufacturers
- Piston compressors from Atlas Copco as well as all reputable manufacturers
- The Oxceo EcoPrevent systems from Minimax
We will send trained and certified personnel with the required professional expertise to you to provide optimal support for your system. In this regard, it is irrelevant whether different system manufacturers are being used. We provide you with comprehensive service independent of the manufacturer.
After each maintenance programme, your systems will be thoroughly inspected as per the particular manufacturer’s instructions and its actual state documented. Thanks to the seamless documentation of your system, we are always able to document its current state and, as a result, can respond to forthcoming events well in advance.
You are always our top priority! The constant availability of your system is our highest priority – day and night.
All servicing work will be calculated according to our fixed maintenance fees. Necessary servicing and maintenance measures will be
carried out by our trained team.
During the maintenance of your system, every single important parameter such as residual moisture is measured and its overall functioning determined as a result. Thanks to professional maintenance, the quality you require for your compressed air is guaranteed.
The scope of service pacakge includes the following maintenance of your compressed air processing unit
- Cold and heat regenerated adsorption dryers from all manufacturers
- Compressed air filtration
- Oil / water separation devices made by Atlas Copco, Beko and Hankison
- Condensate drainage
- Assembly
Competent installation and assembly and the optimal design of your system with respect to energy consumption mean that we can increase energy efficiency. We offer a variety of pipe systems for the planning and realisation of the supply network.
We would be happy to perform a demand measurement for your existing system free of charge to show you the potential opportunities for energy saving. Often the replacement of an old system with a speed-controlled compressor system will amortize itself within just a few months.
We would also be happy to advise you on leakage detection and energy conservation with the use of compressor control systems. These are important components for the introduction of an environmental management system in your company.
As a certified service provider, we can provide you with maintenance agreements that have been precisely tailored to your company’s needs. In this way, you can be certain that your system will always function correctly and reliably and you will also achieve complete transparency with respect to costs into the bargain. Depending on the service agreement, maintenance measures will be charged for at fixed maintenance rates – irrespective of how long the service actually takes.
Our service agreements can contain the following services:
- Maintenance according to the manufacturer’s instructions
- Fixed servicing and repair charges
- Overhaul of motor, gearbox and compressor
- Tool maintenance for pneumatics
(Service and accident prevention regulations on pit lifts) - Service and maintenance of spring balancers
An extended warranty for new systems up to a maximum of 60 months when entering a service agreement creates a firm foundation for working together, and also demonstrates that we only provide you with high-quality components as part of our product range.
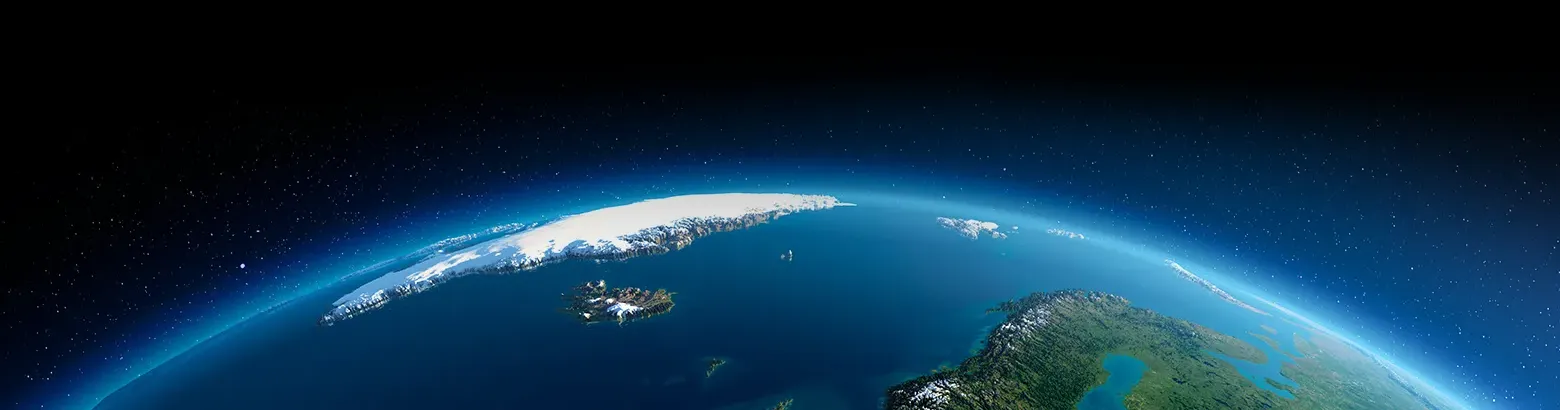